Having
decided which set of screws was which, as they didn't tie in with
the instructions, the pump simply bolts to the left hand running board.
I've left the piece of tape over the outlet in place for now as
there's a small spring and ball in there which I'll probably lose
otherwise. 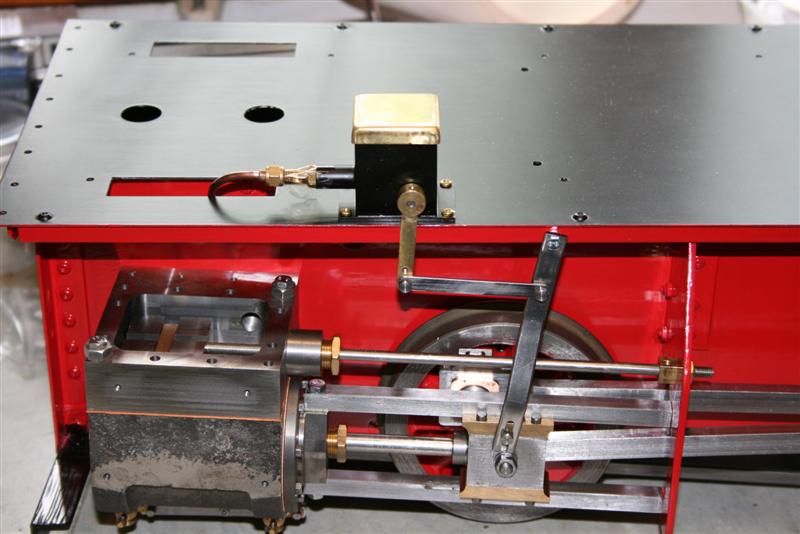
The
forked lever is secured to the edge of the running board by putting the
bolt through the lever, fitting one nut, pushing the bolt through the
running board edge and then fitting a further nut to secure the whole
thing. The two nuts either side of the running board edge are
adjusted so that the lever can move freely. The fork can then be fitted
behind the head of the special bolt on the side of the crosshead.
There's no way of fixing this bolt, except with loctite, so
that there's enough play for the lever to move with the crosshead.
Next, bolt the link between the fork and the pump lever using the two special bolts supplied.
The
last job is to bend the copper pipe between the pump and the oil check
valve on the steam tee. I wasn't looking forward to this as I was
convinced I would kink the tubing. However, with the steam tee
temporarily in place, I carefully bent the tubing bit by bit and was
pleasantly surprised how straightforward it was. The copper is
very soft and bent easily under my thumbs. It's a bit tortuous
passing the pipe through the side frame and down to the check valve but
it looks OK to me. I can't fix it permanently until the steam tee
is fitted.
Kit 5D The DraincocksThe
draincocks and most of the linkage was supplied with Kit 4 but I
elected not to fit them at that point as I felt they would be rather
vulnerable, being low to the bench top while I was working on
other parts. Now was the time to fit them however. First
challenge is to fit them so that they are reasonably tight and all
facing the same way. They are marked Left and Right so that bit
is easy. Wrapping PTFE tape around the threads is very fiddly as
they are so small. Varying the amount of tape and by trial and
error, I eventually managed to get them all in place with the levers
all on the inside and in line.
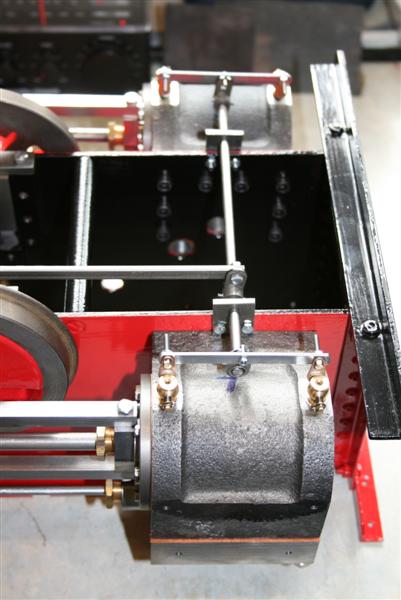
Next
was to fit the link between each pair. First, fit the headless
bolts in the centre of the links that will go into the fork of the
actuating lever. Next pass a bolt through the draincock lever
into the threaded holes in the end of the link. Here's where I
struck a snag as the bolts supplied would not go through the draincock
levers nor into the threaded holes at the ends of the link. It
turned out, after talking to Andy, that the threaded holes had been
cut too small. A replacement set was sent and on we went.
I had to open out the holes in the draincock levers however, as
the bolts would not go through them.
Then bolt the draincock
shaft in place across the frames with the actuating lever on the left
and the pins on the links located into the forks on the shaft.
Now
we move onto the parts supplied with kit 5D which is the actuating
lever for the cab floor and the rod to join it to the draincock shaft.
I found this part a bit tricky as my copy of the instructions had
very poor photos and it was not at all clear which bolts went
where. After a bit of trial and error I got it all together and
the lever in the cab floor moves the draincocks quite easily.
Several of
the bolts have no way of locking them to allow movement of the parts in
operation without it all falling apart again. Obviously, you are
expected to secure all this with Loctite although that isn't mentioned
anywhere. Up to this point, I had deliberately not done that as I
wanted to be sure I'd got everything fitted correctly first. So
now it was a matter of going back over all the nuts and bolts and
securing them with Loctite, at the same time cutting off the surplus
bolt length at the draincock levers.
So there we are, all
parts except the steam and exhaust tees have been fitted and the Kit 5
box is finally empty. I'm looking forward to Kit 6 which has the valve
gear and smokebox and saddle I understand. Hopefully that will be
here in the next week or so and we can finally try to run it on
compressed air. I still have a nagging doubt over a slight tight
spot when turning it by hand but we shall see!
Until the next time...