Andy has sent me
this kit early so that I can get as much done for the POG rally at Peterborough on September 12th as
possible. Geerlig will be there and I am very keen to show him and Andy how far I've got and how I'm making out as a novice builder.
The instructions aren't quite ready yet, but I do have lots
of photos showing where things go. Each pipe
is numbered and I have a packing list with a description so I just need
to
sit down and study everything to decide what goes where. I will also need to clean up some of the excess solder on the tanks in the time remaining, a proper preparation for painting will have to wait until I get back.
This
kit contains the two side tanks and lids, hand pump, whistle and whistle valve,
safety valve, injector, blower valve, pump bypass valve, turret and
water gauge, all the pipe work and finally the cylinder covers.
September 6thI
decided to start with the fittings to the boiler. I had some
photos from Geerlig, and of course my trusty Polly 2 to work from so I
felt fairly confident. I found that I had to remove the
firebox door to fit the clack valve on the lower right hand side of the
boiler backhead. Not a big job but there's limited room to swing
a spanner so it might be better to leave the door off until after the
clack is fitted.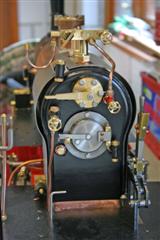
Not
a lot else to report really, just a matter of fitting parts together
with PTFE tape (why does that tape reel always drop onto the floor at
the crucial moment?)I decided that I would leave the water gauge glass off for now in case it gets broken during the build.In
this picture you can see on the turret from left to right, the pressure
gauge syphon, the whistle valve, steam feed to blower valve, and
the steam valve to the injector. Below the firebox door is the
clack for the injector water feed to the boiler, on the left is a
blanking plug.I'm
now working on cleaning up the side tanks - there's a fair few blobs of
solder in awkward places like where the tank covers need to sit flat on
the tank tops - that is going to take some time. I hope to get
one tank mounted before I leave for the Polly Owners Group (POG) Rally at
Peterborough this weekend, but I'll take what I have done so far
and see what others think - not all complimentary I'm sure but
hopefully lots of constructive advice. October 16thBack
from the POG rally, I've decided that I'm going to leave cleaning up
the tanks for painting until later and make a determined
effort to get the engine into steam as soon as I can. I don't
have the ashpan and grate as, strangely, this is part of kit 10 which
is as yet incomplete. I can however, borrow these from my Polly2
assuming they are the same size. But first I had to complete the pipework.
First
problem was trying to get the whistle steam pipe down between the
footplate and the back of the boiler. There wasn't enough room to
get the olive and backnut down through the small gap so I loosened the
bolts holding the smoke box saddle in place so that I could carefully
lift the boiler to get a larger gap.
That
done I turned to the injector pipework. I didn't have any
pictures of how this was to be fitted but after a bit of thought and
studying the lengths of pipes, I decided how it should go. Then the
next problem, the injector to boiler feed pipe wouldn't go through the
gap behind the boiler as it is much larger than the whistle pipe.
Lifting the boiler didn't help so I had no alternative but to
remove the footplate. That however was partly obstructed by the
reversing quadrant which I was not going to undo!
After
a bit of fiddling around, I managed to get a large, coarse round file
onto the edge of the footplate behind the boiler to make a half
round cut out to allow the pipe through. This picture shows how
both these pipes pass through the footplate. Footnote:
I've talked to Andy about this and it seems there maybe a slight
difference in the size of the gap behind the boiler, depending on who
makes the boiler. I've added a note to kit 8 to suggest that you trial
fit the boiler and smokebox to check the size of the gap before bolting
everything down. You may or may not have to make the cut-out, but do
check.
And
so onto the injector itself. After getting it round the wrong way
at first (well you've all been there haven't you?) I worked out where
the pipe runs were meant to go. The water feed is obvious when
you have the tank in place, it's a 'U' shape dropping down through the
footplate.
The
steam feed was not so obvious at first but goes forward, through a
cutout in the running board behind the tank and then up to the steam
valve on the turret. The boiler feed from the injector swings
round behind the reverser quadrant and up to the boiler clack through
the newly created cut out in the footplate. These pictures show it more clearly and you can see the connection with the boiler clack in the picture above.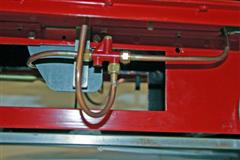
I
hasten to add to all this that the instructions for this kit are
now complete so that the guesswork I used will not be needed when
others get to this stage. Being a "Pioneer" (in other words too
impatient) has its challenges!October 20th
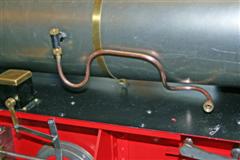
After refitting
the boiler clacks I could then complete the bending for the left hand
pipe work which connects the hand pump in the side tank to the boiler.
This took many attempts before I was satisfied. This
picture shows the tortuous shape of this pipe.
Fitting
the handpump and pipework is next and this turned into quite a
challenge. There's not a lot of room inside the tanks and into
the left hand one has to go the hand pump and its pipe connections to
the boiler, the axle pump bypass valve and its internal delivery pipe
and fittings, plus the fitting to supply the axle pump itself.
If you've got very large hands then it's probably time to
seek out someone with smaller ones!
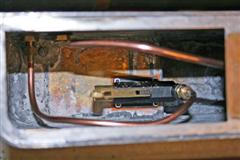
After
some grazed knuckles and a few choice words, I did manage to get
everything into place. It's not easy to take a photo of the
inside of a tank but this will give you an idea. The long
pipe coming in from the right at the top is the axle pump bypass
delivery pipe. It's there to prevent water being pumped out the top of
the tank, apparently.Remaining
jobs were to fix the tanks in place on the running boards and couple up
all the pipework. That also took quite a while as some of the
fittings are in quite an awkward position. I admit that I'm
beginning to wonder if I've done the right thing in not working
on the tanks to clean them up first. I think I'm going to have to
undo much of this work in order to prepare them for painting.
That's another downside of being an impatient person who is keen
to see the engine in steam! Oh well, too late to stop now!Looks
like it will be a week or so before I can find time to meet up with
Paul (my expert friend from earlier) when we will try to raise steam
for the first time. In the meantime I've added a bit more to the
kit 10 page.November 4thSuccessful first steam but with a few mistakes are described here First SteamBack to kit 8
Home
On to kit 10